What are the slag discharge methods for pyrolysis equipment?
Slag discharge methods in pyrolysis equipment are critical for the efficient and safe operation of the process. The slag, also known as char or solid residue, is a byproduct of the pyrolysis process. Proper slag discharge is necessary to maintain the integrity of the pyrolysis reactor and ensure continuous operation. Here, this passage will have a detailed introduction about the common slag discharge methods for pyrolysis equipment based on the degree of automation and discharge location of slag discharge:
1. Degree of automation of slag discharge
(1) Gravity Discharge:
Utilizes gravity to allow the slag to fall out of the reactor through a valve or gate, which has a simple design and is easy to operate;
(2) Automatic Discharge
One method involves using mechanical devices to remove the slag from the reactor. For example, a water-cooled slag discharge auger conveyor can be used; The other method refers to the automated systems that control the slag discharge process, often integrated with sensors and control mechanisms. These two methods can enhance the work efficiency and safety of the whole operation process and save labor and time cost.
Automatic discharge of DOING pyrolysis equipment
2. Location of slag discharge
According to the discharge location of the slag discharge, here are mainly these slag discharge methods: front slag discharge, side slag discharge and rear slag discharge.
(1) Front slag discharge
Front slag discharge is a commonly used slag discharge method in the market because it is easier to operate and has a lower purchase price. According to feedback from DOING customers, slag discharge can be started at about 200 to 300 degrees, and it can be completed in an hour. However, the disadvantage of front slag discharge is that because the slag is discharged at the furnace door, the pyrolysis equipment will look dirtier and the environmental protection level is slightly lower.
Front slag discharge for DOING pyrolysis equipment
(2) Side slag discharge
Side slag discharge is to open a slag outlet every 180 degrees on the side of the furnace of the pyrolysis equipment. When the furnace cools down to below the specified temperature, the furnace door is opened to discharge the slag. The furnace can discharge the slag twice per revolution, which is very efficient. However, the side slag discharge method of the pyrolysis equipment also has many limitations. For example, it is necessary to reserve some space on the side of the pyrolysis reactor to dig the foundation for storing the pyrolysis solid products.
Side slag discharge for DOING pyrolysis equipment
(3) Rear slag discharge
Generally, a spiral auger + ball valve is required to complete the carbon black slag discharge for the rear slag discharge method, which is simple to operate and very trouble-free, and it is not easy to pollute the equipment.
Rear slag discharge for DOING pyrolysis equipment
Now you have a brief learning of the different methods for slag discharge, and if you want to select a suitable slag discharge method, you also need to consider other factors, such as processed raw materials, pyrolysis equipment types and other factors:
• Raw material Types: Different raw materials may produce varying amounts and properties of slag, influencing the choice of discharge method. Take the aluminum plastic as an example, it is not suitable for the rear slag discharge, because after pyrolysis, we can obtain the large aluminum block, which can't be discharged with the rear discharge method.
Various raw materials for pyrolysis equipment
• Pyrolysis equipment types: The design of the pyrolysis equipment(e.g., batch type vs. continuous type) can affect the feasibility of certain discharge methods.
• Environmental Regulations: Compliance with local and international regulations on emissions and waste management may influence the selection of discharge methods.
In summary, there are various slag discharge methods for pyrolysis equipment, if you have any other questions, just feel free to contact DOING, DOING sales manager will provide a detailed scheme for you!
Prev:Can pyrolysis plant be used to recycle waste oil into diesel?
Next:Can waste cable sheath be recycled? What's the recycling process?
Tyre pyrolysis oil is increasingly used as industrial fuel in the market, but unrefined tyre pyrolysis oil contains a lot of impurities and is not effective, so it is better to be distilled to improve the quality of the oil.
Waste oil refining plant is specially designed for waste oil and pyrolysis oil to diesel. This whole refining process includes distillation, cooling, decoloring and deodoring system.
DOING company is strong and has other different processing capacity equipment to choose from, 500kg, 1T, 3T, 5T, 10T. , 12T, 15T, 30T, 50T, 100T, and so on. Compared with these large capacity equipment, small plastic to fuel machine also has its unique ad
Please feel free to leave your contacts here and your privacy is protected. A competitive quotation will be provided according to your detailed requirement within one business day.
-
Tel/WhatsApp: 0086-135-2669-2320
-
Phone: 0086-371-5677 1821
-
Skype: bonniezhao2
-
E-mail: sales@doingoilmachine.com
- What are its plastic pyrolysis benefits compared to traditional plastic recycling methods?
- How pyrolysis technology helps reduce the carbon footprint?
- Can you get money out of old tires?
- What is the Most Profitable Plastic Recycling Way?
- How to Set Up a Tire Pyrolysis Recycling Business?
- Why is PET and PVC not suitable for pyrolysis?
- How much oil gas is generated during the pyrolysis of plastics?
- How to Improve the Quality of Plastic Pyrolysis Oil?
- Equipment composition of waste plastic oil pyrolysis production line
- What are the types of materials pyrolysis equipment can process?

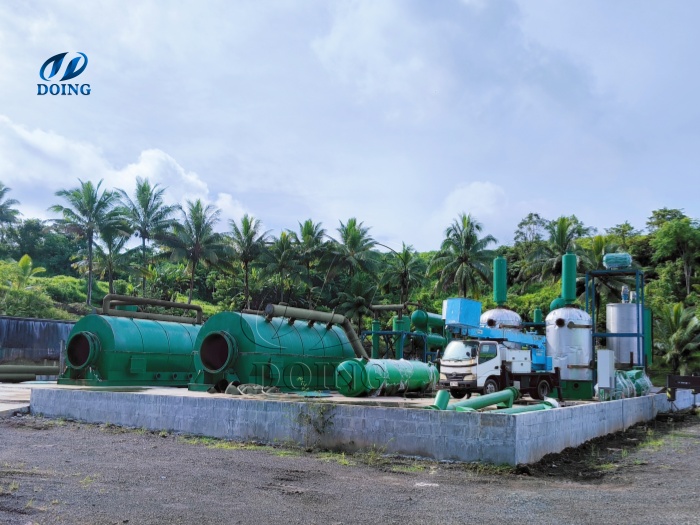

Leave a message
Mobile/Wechat/Whatsapp: